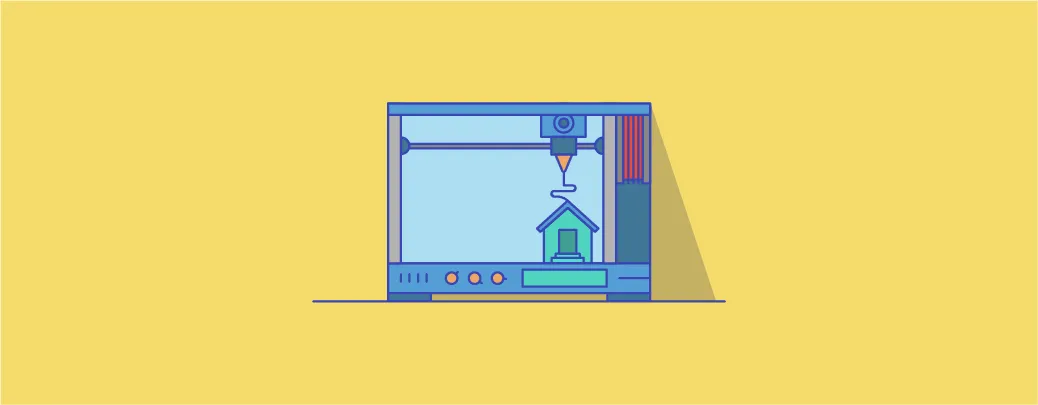
I used to be a stone mason. I’d mix concrete in wheelbarrows, lug rocks around and shape fridge-sized sandstone blocks with a mallet and a chisel. I loved it. I was out in the sun with some great blokes and ham sandwiches never tasted better. But working in a limited market meant jobs started to slow to a trickle. Because we were ‘purists’ (read: luddites) who did everything by hand, our work could take months to complete - and that made it expensive. Too expensive for most people to afford.While hand-crafted, artisanal sandstone sculptures aren’t exactly a necessity for your average family - housing is. And the same formula carries through. It costs a lot to build a house - and most of that comes not from materials, but from labour. The $8.5 trillion dollar global construction industry is hardly known for its efficiency. Yet as the world population increases, we’re going to need to put roofs over heads - and, as per usual, technology is here to save the day. We’re finding more and more ways to reduce the labour required - and thus the price tag - on a freshly-minted house.
CNC machining
As we’ve already laid out in our previous post on open source architecture, CNC machining (Computer Numerical Controlled) has huge potential in the construction industry.In a nutshell, CNC means that rather than having an operator on a lathe, for example, you can feed the plans into a computer and have it do all the work for you. Computers are fantastic at both speed and precision - so they’re worthy prodiges to even the most experienced machinists. And the applications are endless: mills, drills, jig-saws, plasma cutters - you name it. Now, the operator has to merely load the designs into the computer and rest of the work is done automatically.What’s more, some forms of CNC (such as jig-saws) are portable. This means they can be brought directly onto the job site, and work can be carried out there - removing another trip for truck-drivers, and mitigating the risk of time consuming accidents such as the wrong dimensions being cut.CNC is the ultimate labour saving device - and the implications are huge for people from all walks of life. From erecting quick, cheap housing to alleviate homelessness after earthquakes, to reducing the cost of crisp, contemporary homes - CNC is already here, and here to stay.
3D printing
3D printing, (technically another form of CNC machine), is often touted as a bit of a gimmick. 3D printing works by programming a nozzle to follow a set path and apply, layer by layer, whatever material you want to ‘print’. By stacking layers on top of one another, it can create three-dimensional objects. Mattel - creator of Barbie and Hot Wheels toys - recently released a 3D printer of their own: The ThingMaker. The sole purpose of which is to allow children to print out whatever stomach-churningly twee plastic figurines they want. But 3D printing is far from a novelty. In fact, used correctly, it might just be one of the biggest breakthroughs we’ve had in construction in the last decade.Imagine if we took Mattel’s ThingMaker, made it a few hundred times bigger and got it to print in concrete rather than brightly coloured plastic? That’s exactly what Andrey Rudenko and his team have created: the world’s first ‘3D concrete house printer’. The results are amazing.Rudenko’s house printer isn’t just an experiment anymore. The Lewis Grand Hotel was Rudenko’s first customer, and is now home to the world's first 3D printed commercial structure.Their new suite includes two bedrooms, a living room, and even a giant 3D printed Jacuzzi. After testing with parts and materials, Rudenko told 3ders.com; “It took some time like several months to set up everything but now we are able to print a medium size house here in about a week using local cheap sand including plumbing and wiring.”A week. If only you could print sandstone.
Drones
Goldman Sachs recently released an assessment of eleven industries drones are set to affect the most. Construction was number one - almost doubling agriculture’s (number two) total addressable market for the technology.How could this be? What role do drones have in construction?From a property planning perspective - drones are a huge benefit to surveyors. Satellite imagery is often outdated and not-nearly of a high enough standard to have any serious applications. Bird’s eye view imagery was often handed over to expensive helicopter teams for large scale developments. Not any more.Now, companies like Skycatch use drones to capture aerial footage, and turn it into stunning 3D models. Builders can use their software to create structural models, topographical maps, and volumetric measurements. These are useful for monitoring stockpiles of costly resources like sand and gravel, for instance, hence saving you money on materials.Then there’s Kesprey, who specialise in using drones to survey job sites and track progress. Giving construction companies quite literally the ‘big picture’ allows them to deploy resources more efficiently, minimize potential impending issues and limit delays. Ergo; cut costs.And if all that wasn’t enough - here’s a fleet of French drones building a tower out of styrofoam. Which brings us to the biggest potential cost-cutter of all. Replacing tradespeople with robots.
Robots
Robots. Pretty straightforward really. They work for free.McDonald’s, battling employees recent demand for $15 and hour, are looking to simply swap them out with robots. The construction industry could potentially go the same way. While this might seem like a terrifying reality to most, construction robots aren’t going to just be recreating the same burger a thousand times per day, so we can be pretty comfortable the job losses probably won’t be quite as severe. All the same, it’s something to keep an eye on.An Australian technology company, Fastbrick Robotics, are building - you guessed it - the world’s first bricklaying robot: the Hadrian X robotic. It’s designed to automate the loading, cutting, routing and placement of bricks - a feat which they assert will ‘transform the construction industry’. They might be right, too. Their truck-mounted, robot arm can place 1,000 bricks an hour.Pretty soon, the cost of building might not be too much more than the price of materials alone - and this is going to boost the residential and commercial real estate sector by several orders of magnitude.
More or less affordable?
Skeptical readers might be asking themselves whether these new technologies be able to help us create more affordable housing, or simply kill jobs and line fatcats’ pockets?‘How much progress is too much progress’ is the question asked whenever anything gets automated and jobs are on the line. But is that even a viable question? Throughout history, technology has only ever laid out a positive narrative. Here’s how progress (generally) works:
- Technology substitutes labour. This, in turn, raises productivity - and increased productivity means lower prices. The invention of the personal computer, for example, removed the need for much of the administrative grunt work and cut costs drastically.
- The sectors behind the technological innovation expand. Whenever an industry expands, new jobs are created. While there might not be many people filing anymore, consider the rapid and sudden demand for software engineers over the last ten years. An indirect effect, new technologies serves to complement labour in other sectors - which in turn boosts employment and further benefit humanity’s advancement. Just look at what the advent of computers and software has done for medical research.
Over the last 200 years, new technology has rendered industry after industry obsolete. But paradoxically, employment has risen faster than ever before. The United Kingdom has more than doubled its employment in the last 150 years - and it’s far from the only place to do so.Plus, greater efficiency and lower prices mean people have more money for discretionary spending. You know; treating ourselves. There’s a reason the entertainment industry is booming, far fewer households cut their own hair, and gyms are popping up on every street corner.If we follow the same trends we’ve seen in other industries and sectors, the rise of technology in construction won’t end the world, and will radically drop the cost of building a home. Sure, over time, bricklaying might no longer be a viable career option, but there’ll be countless jobs building, servicing and improving automated construction technologies. Don’t sweat it.Although these technologies are still in their fledgling stages, thanks to the miracle of capitalism, they will lower the cost of construction. Construction and real estate have always been intrinsically linked. Land sales will rise and there’ll be more stock for real estate agent’s shelves. It’s a bright future ahead for housing. Sadly, the same probably can’t be said for old-school stone masonry. Hey - you win some, you lose some.